Spencer Garrett-Construction Option
AE CPEP Thesis

Building Statistics 1
Project Information
Building Name: 160 East 22nd
Location: New York, NY
Building Occupant Name: Condo Owners, Renters of Retail Space
Occupancy and Function Types: Primarily luxury condominiums with retail space, fitness center,
and a daycare center
Size: 114,000 GSF
Number of Stories above grade: 21
Dates of Construction: May 2012–May/June 2014
Cost: 40 million overall cost, 33 million building cost
Project Delivery: Design-Bid-Build
Project Team
Owner and GC: Toll Brothers [www.tollbrothers.com]
Architect: S9-Perkins Eastman Architects PC [www.perkinseastman.com]
Structural: Gace Consulting Engineers PC [www.gace.net]
MEP: Dagher Engineering, PLLC [www.dagherengineering.com]
Lighting Design: Lighting Workshop [www.ltgworkshop.com]
Civil Engineer: AKRF Engineering [www.akrf.com]
Acoustic: AKRF [www.akrf.com]
Architecture
160 East 22nd is one of Toll Brothers latest additions to their line of luxurious high rise condos in the City Living Division. Located in the historic and up to scale Gramercy District in New York City, these condos try to bring an urban feel to an older neighborhood. The building carries a unique offset design. The building carries roof penthouse floors on different levels. This gives off the jagged-like facade. Most notable is the 24 foot cantilever that reaches over a set of existing buildings. The entry level will offer a gym for the residents and also a child care center.
-
Major Codes
-
NYC 1968
-
FHA and ADA compliant. Years not specified
-
-
New York City Zoning
-
C2-8A:Retail
-
C1-9A: Multiple Dwellings
-
Total Zoning Lot Area-12,773.8 SF
-
-
Historical
-
There are no historical requirements for this building
-
Building Enclosure
Façade: The façade of the entire building is a precast engineered limestone cladding system. The cladding system manufactured by StoneLite is a hybrid natural and synthetic stone. A thin layer of stone is backed by two layers of epoxy skin, and an aluminum honeycomb shell. All of these parts are designed to shed water from the inside of the building, and hold up the layer of veneer. The cladding is attached to the building using a concrete curb cast on the deck using metal clips and backer rod. Painted aluminum windows are set on top of the curb and are caulked and sealed using a fireproofing material called Thermafiber to fill in the window areas that do not have direct light access to the outside
Roofing: The roofing system is a 2 ply modified bitumen membrane that is lies on top of the structural slab. A drainage mat fixed to the membrane line 4” polystyrene rigid insulation above. The drainage mat is tied to drains that are cut into the finishes on the roof. The finishes for the private roof terraces are concrete pavers, and wood decking.
Sustainability
There are several sustainable features in the building. Some of the more common passive systems are bike racks located outside of the building to discourage the use of fossil fuel vehicles, and the use of Astroturf grass and drought resistant plants on the roof terraces which reduce water use. Active systems in the building comprise water reducing appliances such as flow-reduced lavatories, and low-flow showers. Another active system is the use of HVAC systems that do not use Chlorofluorocarbon based refrigerants that harm the ozone. Current systems are scheduled to not have these toxins and carry a good enough EER score to meet LEED Certifications.
*All photographs courtesy Toll Brothers GC LLC*
Building Statistics 2
Construction
The primary owners of the condo spaces in this building are the condo owners. Toll Brothers is simply a Construction and Sales Manager of the property. Toll makes a profit from the selling of these condos to these owners. The condos are a combination of speculative and custom construction. The owners are committed to paying for the condos before construction, but the only decision that the owner is allowed to make concerning the living space are finish choices and choice of appliances.
A mobile crane and pump truck were used primarily for the construction of the superstructure. Mobile crane was used to carry large materials up the tower, and the pump truck was used to pour the superstructure. The concrete was formed with stripped plywood. A temporary platform was used on the 6th floor to brace and shore the construction of the cantilever started on the 7th floor. Steel beams were used to shore the slab and structures above the cantilever until that portion of the building could hold its own weight. An entire erection plan was executed in order to construct this platform. There was and will continue to be a large amount of linear scheduling used on this project. The time frame to complete the building is very constricting due to the demand of the condo owners, and several spaces especially the fit-out of the condos need to be constructed simultaneously in order to reach the projected finish date.
Structural
The building is twenty one stories with a structural 24 foot cantilever that spans from the 7th floor to the roof on the south end of the building. The structural system consists of conventional reinforced concrete flat plate slabs which is supported by concrete columns and shear walls. Shear walls and moment frames on the perimeter of the building support against wind and seismic loads.
The superstructure is supported on a deep foundation consisting of 260 ton piles. The sub grade slabs are 14” formed slab for the sub-cellar level and 5” slab on grade for the cellar level. These levels are enclosed by 12” foundation walls, and are laterally supported by the slabs. Floors from 1st-6th are 8” elevated slabs. From the 7th floor to the roof the slab increases to 9”. There is a transfer slab on the 16th floor which is 20” thick.
The cantilever portion of the building is supported by 2-story high cantilevered beams extending from the stair and elevator cores. Additionally, there is a diagonal column carrying load to the east on the exterior of the building. The slab at the bottom of the cantilever on the 7th floor is 3” concrete topping on Styrofoam on a 9” depressed concrete slab.
Lighting/Electrical
Consolidated Edison Company will be supplying power to the building in the form of 208 V service. There will be 1 meter that monitors power use of the main building loads such as in the retail space and the gym. There will also be individual meters for each of the condominium units. The electric service will enter the building through the cellar at the north end of the site. The power will be distributed by the main electrical room. There is no transformer in this system.
There are 4 main switches that service building loads and then there is an additional that will serve a 75 horsepower fire pump. The details are listed below:
-
1, 400 amp, 3 Phase , 4 wire switch will feed the future retail space
-
2, 1200 amp, 3 phase, 4 switches will feed the condominium units
-
1, 1600 amp, 3 phase, 4 wire switch will serve base building loads
-
1, 1600 amp, 3 phase, 3 wire switch will serve the fire pump
Each condominium unit will contain a single phase, 208 V circuit breaker panel. The commercial space will contain a 400 amp, 208 V 3-phase panel.
The condominium units will be provided with commercial grade ceiling light fixtures for the common areas such as foyer, kitchen, bathroom, etc. These fixtures will be mostly recessed circular compact fluorescent and LED lighting. Other lighting fixtures will be provided by the homeowners. The residential lobbies and entrances will be provided with recessed down lights, cove lights, surface mounted strip fluorescent lighting and suspended seamed cast glass spheres.
Cellar and Sub-Cellar mechanical areas will be lit with pendant or surface mounted fluorescent lighting with emergency battery pack which will be controlled by a light switch. Corridors will be lit with recessed LED down lights.
Mechanical
The building’s mechanical loads will be served by Consolidated Edison Company in the form of gas. There will be 2 meters. One will be used to monitor the building heating and domestic hot water boilers. The other meter will be used to monitor stovetop cooking in the condominiums. Heating will be provided by boilers and circulated by heat pumps. Each condominium will be served by water source heat pumps. Some may have multiple pumps depending on the loading of the space. Master bedrooms have their own heat pumps with individual control. Shared and amenity areas will be served by dedicated water-cooled heat pumps.
230 ton cooling towers on the roof of the building will provide condenser water for the building to service A/C for the building. The water will be circulated using condenser water pumps, and the same water source heat pumps will be provided in each of the condominium units.
All bathrooms will contain mechanical exhaust fans, and the bathrooms in each condo unit will be provided with constant air regulators that will maintain continuous exhaust.
Fire Protection
Wet pipe, J-2 sprinkler alarm systems will monitor the building’s fire devices. These include sprinkler and fire pump flow, smoke detectors and heat detectors for boilers. Combination smoke and carbon-dioxide detector will be placed in all living spaces. Smoke detectors will be provided in Electric Rooms and the top of elevator shaft, top of stair shafts, telephone, and Elevator Machine Rooms and heat detectors at boiler room. System will also include flow and tamper switches for each floor sprinkler system including compactor chute and vestibule.
Transportation
2 passenger elevators serve the building with capacity up to 2500 pounds. There is also a main stair well centrally located in the building that contains 2 adjacent staircases.
Telecommunications
Telephone, cable, and data service will be provided to each condo unit by means of wiring from the sponsoring company’s panel located on every 4 floors starting on the 4th floor. Each panel feeds individual locations within the living spaces. The commercial space is equipped with 2 2” empty conduits from the main telecom room to junction boxes where future tenants can install services as needed or required.


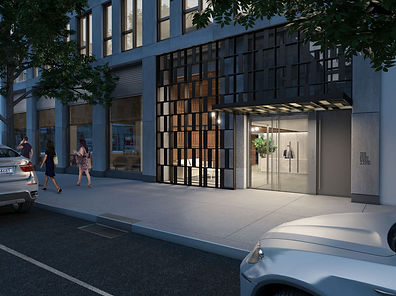


